Unlocking Efficiency in Manufacturing with the Best Sheet Lifters and How to Choose the Right One
In today's fast-paced manufacturing landscape, efficiency is paramount, and the role of specialized equipment cannot be overstated. Among these essential tools, Sheet Lifters have emerged as vital assets for increasing productivity and minimizing workplace injuries. According to a recent report by the International Federation of Robotics, the use of automated lifting devices has led to a 30% reduction in labor-related injuries in manufacturing environments. Furthermore, a study by the National Institute of Standards and Technology highlighted that companies utilizing advanced lifting solutions exhibit a 25% increase in operational efficiency. As industries strive to meet both market demands and safety standards, understanding how to select the right Sheet Lifter becomes crucial. This blog will explore the challenges faced in the manufacturing sector and provide guidance on choosing the most suitable Sheet Lifter to unlock unparalleled efficiency.
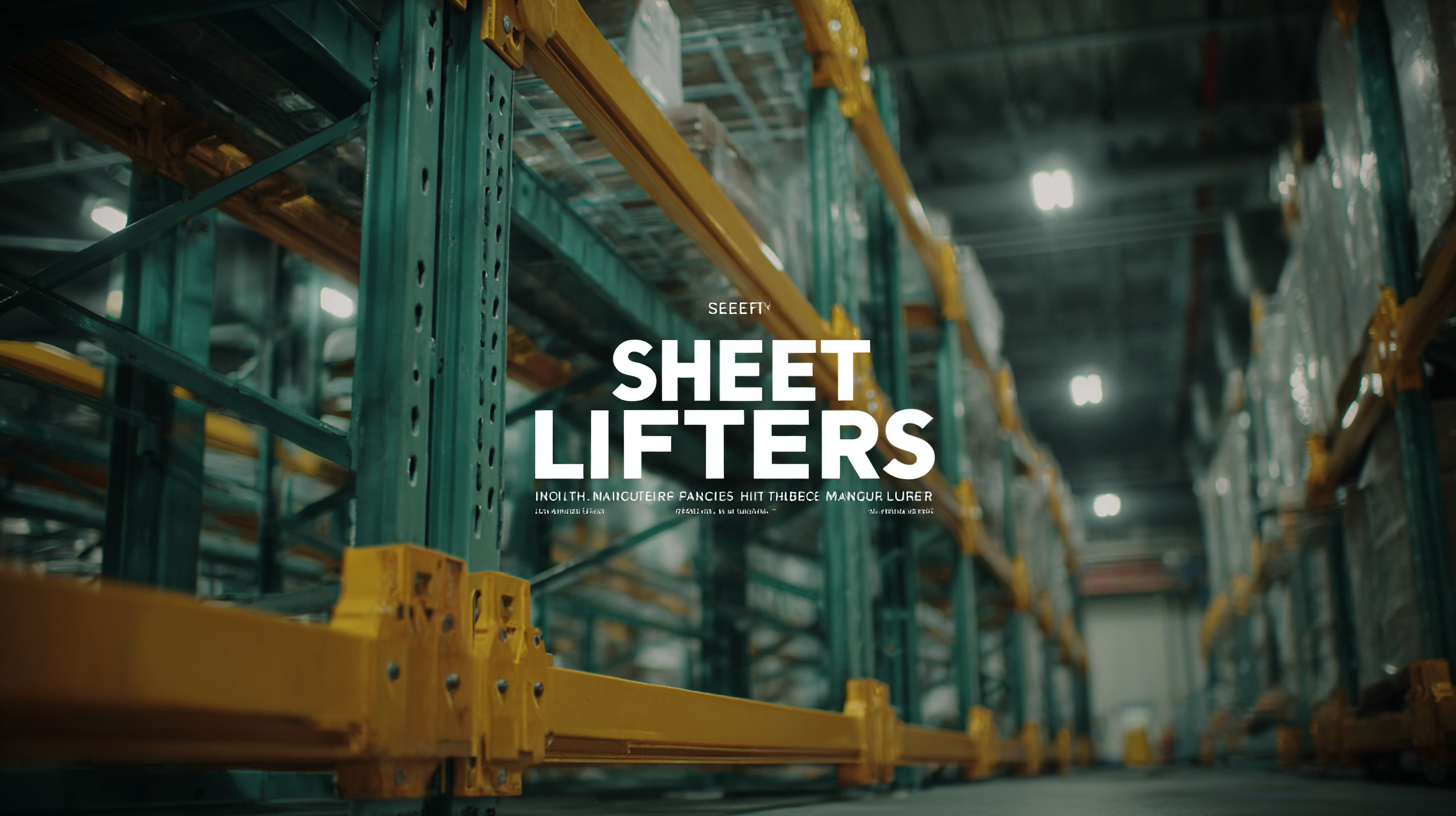
Importance of Sheet Lifters in Modern Manufacturing Efficiency
In modern manufacturing, the efficiency of operations has become paramount, and sheet lifters play a critical role in achieving this goal. These tools are designed to handle large and heavy sheets with ease, reducing the risk associated with manual lifting and allowing for smoother workflows. As industries strive to optimize their production processes, the right sheet lifter can significantly enhance productivity, minimize downtime, and improve safety standards.
Choosing the right sheet lifter involves considering various factors, including the weight capacity, lifting height, and the specific application requirements. Manufacturers must evaluate their operational needs to determine which equipment aligns best with their processes. Similar to how the heavy-lifter vessels in the shipping industry facilitate large cargo movement efficiently, the right sheet lifters ensure that materials are handled swiftly and securely on the shop floor. By investing in high-quality sheet lifters, companies can streamline their manufacturing processes, leading to greater overall efficiency and competitiveness in the market.
Factors to Consider When Choosing the Right Sheet Lifter
When selecting the right sheet lifter, it's crucial to consider several factors that can significantly impact efficiency and safety in manufacturing environments. According to a report by the American National Standards Institute (ANSI), improper lifting techniques can result in a staggering 31% of workplace injuries in the manufacturing sector. Therefore, investing in a sheet lifter that enhances ergonomic handling is essential. Look for features such as adjustable height, load capacity, and grip options that cater specifically to the materials being lifted. By choosing a lifter with these capabilities, companies can mitigate health risks and enhance productivity.
Additionally, the size and weight of the sheets being handled should influence the selection process. A recent survey conducted by the Fabricators & Manufacturers Association (FMA) revealed that 50% of manufacturers reported inefficiencies when lifting sheets that did not match their equipment’s specifications. Selecting a lifter tailored to specific sheet sizes not only ensures optimal handling but also minimizes the time spent on each lift, contributing to overall operational efficiency. Investing in technology designed to accommodate your unique manufacturing needs will yield long-term benefits and increase output.
Unlocking Efficiency in Manufacturing with the Best Sheet Lifters and How to Choose the Right One - Factors to Consider When Choosing the Right Sheet Lifter
Feature | Description | Consideration |
---|---|---|
Weight Capacity | Maximum weight the lifter can handle. | Ensure it meets the demands of your materials. |
Lift Height | The height up to which the lifter can raise sheets. | Match this with your workbench or loading dock height. |
Material Type | Compatible materials such as metal, plastic, or wood. | Choose based on the specific materials you'll handle. |
Portability | Ease of movement and transportation of the lifter. | Consider a lifter that fits your workspace layout. |
Automation Features | Level of automation in lifting and handling sheets. | Assess if you need manual or automated handling for efficiency. |
Safety Features | Inbuilt safety mechanisms like overload protection. | Ensure compliance with workplace safety standards. |
Cost | The total price of the sheet lifter. | Balance quality against budget constraints. |
Types of Sheet Lifters and Their Applications in Industry
When it comes to enhancing efficiency in manufacturing, understanding the various types of sheet lifters and their applications is crucial. Sheet lifters come in several designs tailored to specific industrial needs, including
manual, semi-automatic, and fully automatic models. According to a report by MarketsandMarkets, the global sheet metal fabrication market is projected to reach $484.69 billion by 2026, indicating a growing demand for equipment that streamlines operations and reduces manual labor.
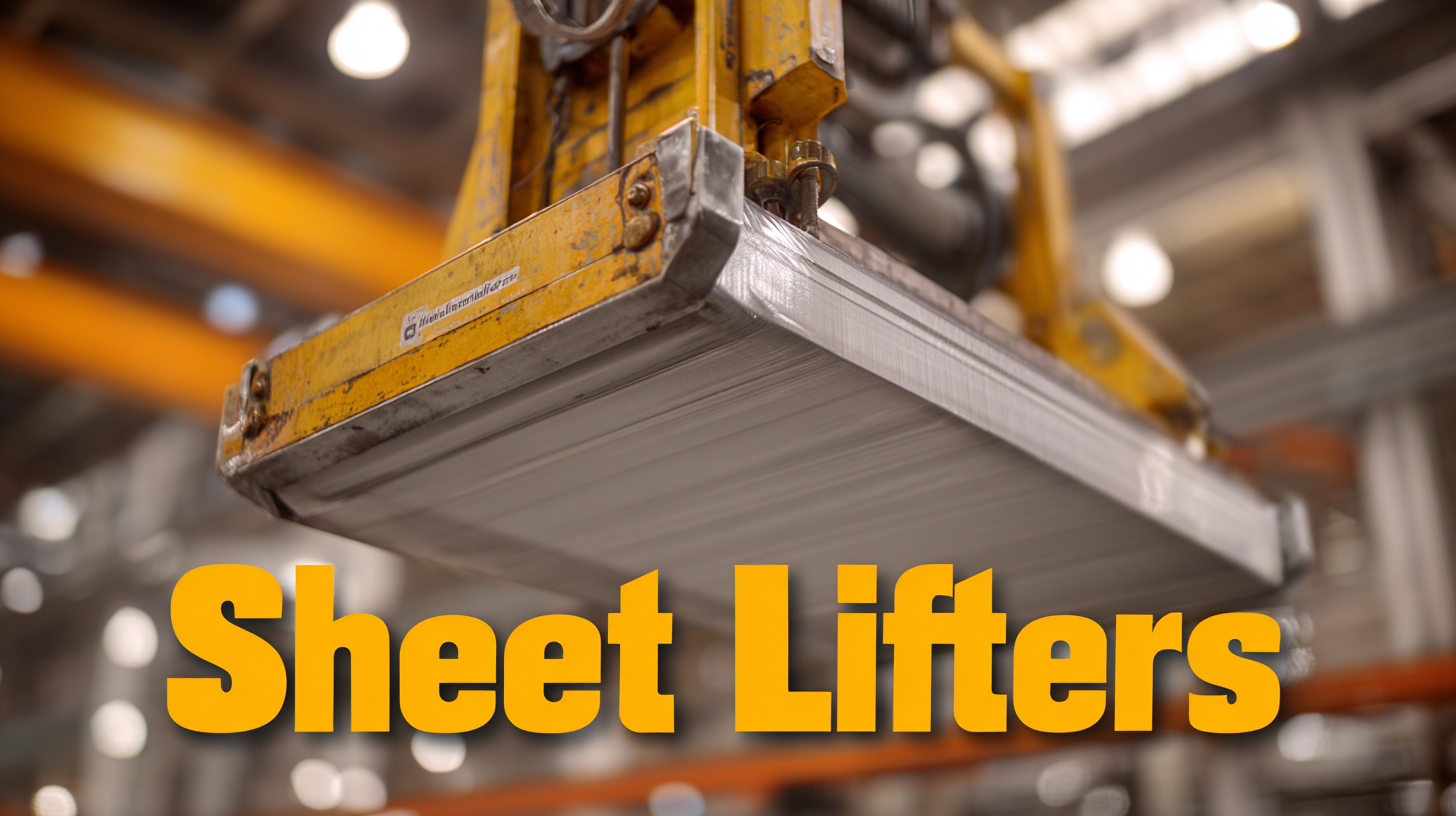
Maintenance Tips for Optimal Performance of Sheet Lifters
Maintaining sheet lifters is crucial for ensuring optimal performance and extending their lifespan. Regular inspections should be a routine part of your maintenance schedule. Check for any signs of wear, such as frayed cables or bent supports, and address these issues promptly. A proactive approach will help prevent unexpected breakdowns and keep your operations running smoothly.
Another essential tip is to keep all moving parts well-lubricated. Proper lubrication reduces friction, allowing the lifter to operate efficiently and decreasing the risk of mechanical failure. Use the manufacturer-recommended lubricant to ensure compatibility with your specific equipment. Applying lubricant at regular intervals will promote longevity and enhance the overall performance of your sheet lifters.
Lastly, it’s beneficial to train your staff on the correct usage of sheet lifters. Providing guidance on safe handling techniques not only reduces the likelihood of damage but also promotes a safer working environment. Regular training sessions can reinforce best practices and keep all team members informed about proper operational procedures.
Case Studies: Transforming Operations with Sheet Lifters
In the rapidly evolving landscape of manufacturing, implementing innovative tools is essential for optimizing operations. Sheet lifters have emerged as a game-changing solution, with numerous case studies highlighting their transformative impact on productivity. For instance, a leading automotive parts manufacturer adopted advanced sheet lifters, resulting in a 30% reduction in handling time. By automating the movement of heavy materials, they not only minimized workplace injuries but also enhanced workflow efficiency, allowing for faster production cycles and improved safety standards.
Another compelling example comes from a furniture manufacturing company that struggled with manual sheet handling. The introduction of sheet lifters allowed them to streamline their processes significantly. Operators could now load and unload heavy sheets with ease, which cut down on downtime and improved overall operational throughput. As a result, they reported a 25% increase in production output while also fostering a more ergonomic working environment. These cases illustrate how choosing the right sheet lifter can unlock substantial efficiencies, proving that investment in the right equipment pays dividends in enhanced operational capabilities.
Unlocking Efficiency in Manufacturing with the Best Sheet Lifters
This bar chart illustrates the impact of different sheet lifters on manufacturing efficiency, measured in productivity increase percentage. The data represents case studies showing how various types of sheet lifters have transformed operations in the manufacturing sector over the past year.